When we started working with PIM systems, this area was relatively unpopular in Russia. He was mainly interested in large companies and representative offices of international holdings, for which product information management was an urgent problem.
I think that interest in such systems would also develop organically, as part of the general trend towards digitalization. But 2020 spurred the PIM market, or rather, forced retail and manufacturing businesses to automate processes more actively.
Why do businesses need a PIM system
Each product can have more than 200 attributes: descriptions, articles, prices, photos, seasonality, discounts, product relationships, etc. These attributes have to be assigned, edited, received, transferred to sales channels and internal systems, updated, and transferred again.
When properly transferred to marketplaces, each attribute can improve the catalog's position or change its connectivity. Therefore, adding attributes or new values to them is a separate business process that requires action in itself. In addition, each attribute can be a separate complex reference book that procurement, production, and suppliers must work with.
Back in 2012, Goodmasters, a research firm, considered that It takes about 25 minutes per year to collect and update data about one SKU. For non-core systems and applications, this figure still remains approximately the same. The speed of entering data, for example, into Excel is poorly affected by what version of the product the manager works in.
If your company has a catalog of 100 SKUs (which is rare, but it happens), you can ignore the time spent on attribute operations. What if we are talking about at least 1000 SKUs?
At 5000 SKUs, the numbers are quite impressive. Using simple calculations, we will get 12 man-months per year spent manually working with data. Conditionally: one of the employees spends ALL of his working time working with product data!
The larger the catalog, the more noticeable the costs of maintaining it and the higher the likelihood of failures and errors due to human factors. All the more business processes are in people's minds, not in information systems. The data quality is all the worse. And the longer the time it takes to bring goods to the market.
PIM system (abbreviated from English product information management system, Russian. “product information management system”) automates the work with product information: control over filling, updating, versioning, sending and receiving data, searching for information, etc. According to the same studies, the introduction of a PIM system reduces the time it takes to collect and update data about each SKU to 4 minutes per year — that's six times less! It also reduces the time it takes to enter the market for certain goods — by three to four times. Another thing is equally important: the quality of data is improving.
In addition to saving time, the PIM system allows you to:
- control the completeness of product data;
- to unify the recording of information about goods, including in accordance with standards to simplify electronic document management (ETIM, GS1, etc.) );
- enrich product information (for example, from external sources);
- collect data from external systems (CRM, WMS, etc.) and send them information;
- send to different sales channels exactly the information and form they need (language, completeness, availability of photo and video materials, etc.) — PxM (abbreviated from English product experience management, Russian. “managing the experience of interaction with goods”);
- record changes and store previous versions of product information;
- give employees different rights to edit information depending on their areas of responsibility.
The world chooses: which PIM systems are popular in the European and American markets
The Russian market has traditionally developed along its own path, albeit with an eye to the world. The scenario with PIM systems is exactly the same: if you compare the Russian and, for example, the American top 10 PIM products, you will find a maximum of three matches between the lists. The rest of the products will be unfamiliar to Russian businesses.
But if you are planning to enter the international market, it makes sense to integrate into your architecture those systems that will allow you to quickly integrate with marketplaces and other sales channels operating in the market you need.
In this article, we are not going to understand what PIM is for manufacturing, retail and hybrid companies. This is a separate complex topic, and we will come back to it later.
In the meantime, we have analyzed which PIM systems are popular not only in the Russian but also in the European and American markets. This is not a ranking of systems, there are no “best” or “worst” ones, so to avoid unnecessary interpretations, we sorted the list alphabetically. So, in this article, we'll look at:
- Akeneo PIM
- Catsy
- Inriver
- Pimcore
- Plytix
- Riversand
- Sales Layer
- Salsify
Akeneo PIM
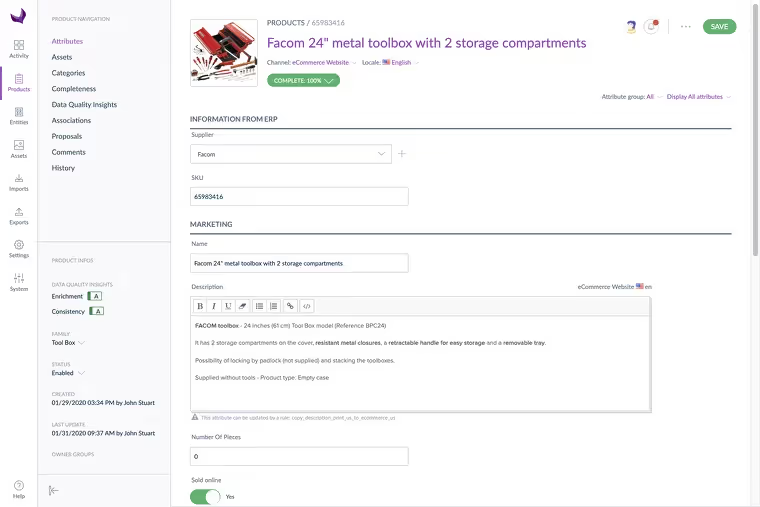
Master system for centralized management of marketing and technical information. PIM system Akeneo more than 500 enterprise-scale companies use it.
Akeneo PIM functionality
Akeneo PIM is a complete PIM system with PxM elements.
- Product data management.
- Manage categories and catalogs.
- Editing tools.
- Automatic and manual addition of product data.
- Change data about several items at the same time.
- Analysis of the completeness and quality of filling out product cards.
- Manage media files taking into account the specifics of channels.
- Manage roles and access (Enterprise Edition only)
Versioning
The history of changes in product data is saved in the system: you can see who changed what and when. The administrator can roll back changes to the required version at any time.
Flexibility and scalability
Open source allows you to scale Akeneo PIM to take into account the expansion of the catalog's nomenclature and the growth in the number of distribution channels.
Additionally, you can install modules for PxM: Akeneo Onboarder and Franklin. There may be improvements at the code level (for the Community Edition).
Who is Akeneo PIM for
Businesses of all sizes. A basic version with limited functionality is suitable for small businesses — Community Edition (code-first, installed on your servers), Enterprise Edition (SaaS) with advanced features will meet the needs of large businesses. In our opinion, in general, Akeneo PIM is not suitable for manufacturing companies and companies with products with highly related attributes due to the lack of functionality in independent directories.
License cost
Akeneo PIM is available in three builds with different amounts of functionality.
- Community Edition. A free open source version with limited functionality. It takes place on your company's servers.
- Growth Edition. A paid version with limited functionality. Cloud deployment, SaaS. Yearly billing.
- Enterprise Edition. A fully functional paid version. Cloud deployment, SaaS/PaaS. Yearly billing.
The cost of an annual license is discussed with Akeneo individually at the negotiation stage.
Catsy
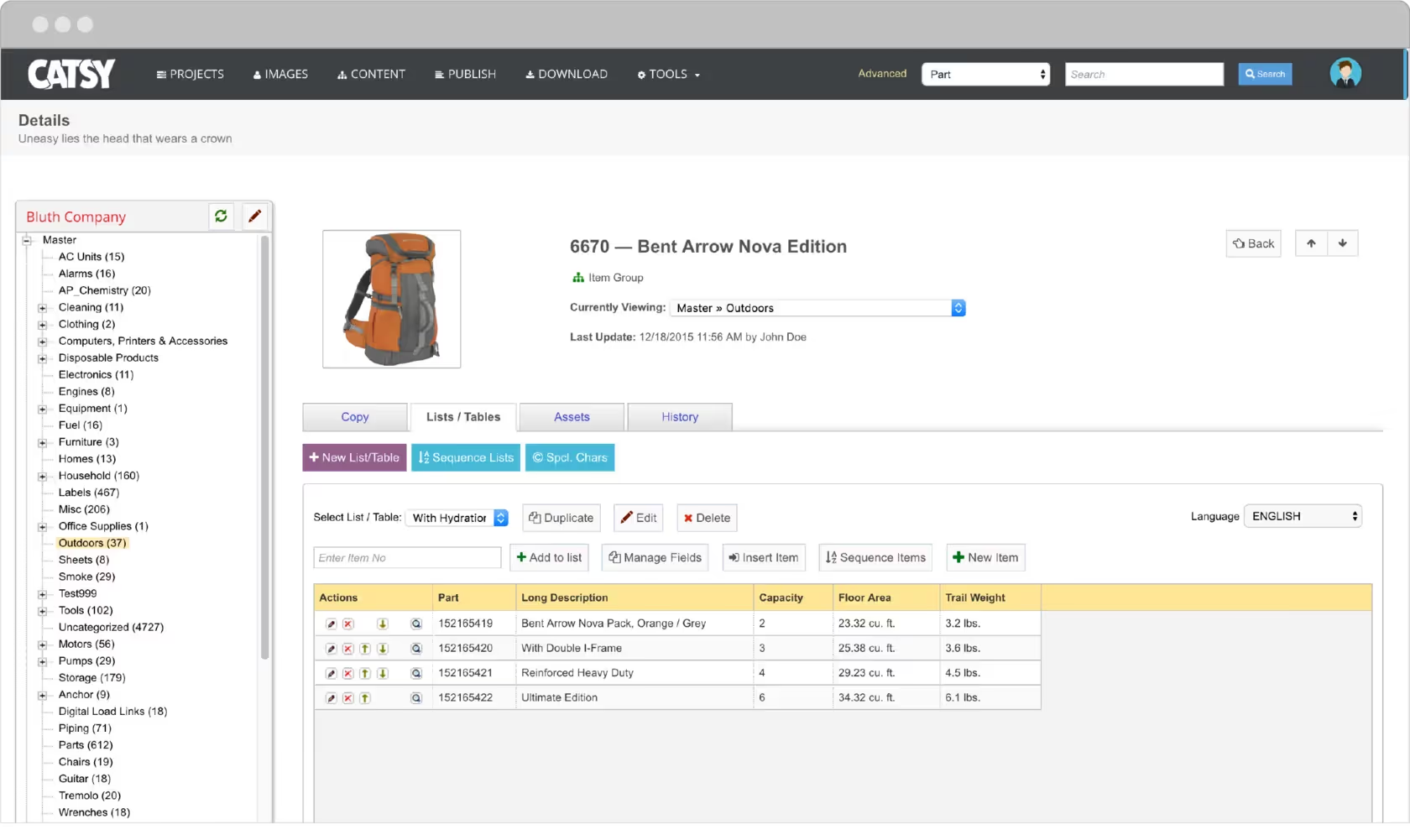
Catsy is a PIM/DAM/PXM system that allows you to centrally manage product information, digital data (photos, videos, etc.) and customer experience.
Catsy features
- Product data management.
- Advanced catalog search system — for quick access to the right SKUs.
- Validation of information.
- Digital data management (DAM).
- Links between products: the system helps the end customer find an alternative if the product they have chosen is out of stock.
- Combining goods into sets, linking accessories to the main product.
- Analytics and reports.
- Managing roles with the assignment of rights to view, edit, and publish information.
- Save content versions to the product card: you can track when changes were made and, if necessary, roll back to previous versions.
Additional features
Quick start. The vendor's successful cases include deploying and launching the system, uploading data on 66,000 items to the system within nine days.
Flexibility and scalability
The Catsy solution is designed for businesses of all sizes. A small company can choose only the modules it needs and add new PIM system modules as it grows.
Who is Catsy for
Small and medium-sized businesses that specialize in the production and sale of goods.
License cost
It is deployed in the cloud (SaaS). There is no free version, but you can order a demo from the vendor to make a purchase decision.
A license is purchased for each user.
Information about the cost of an annual subscription is available on request.
Inriver
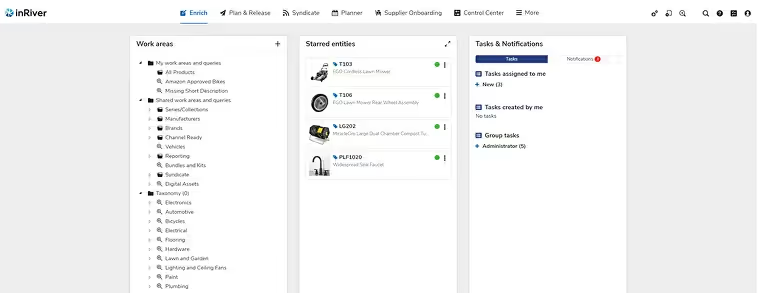
Inriver is a PIM system with sophisticated marketing tools. It not only stores, unifies and transfers information about goods, but also allows you to receive effective recommendations about what influences users' purchasing decisions.
inriver functionality
- Recording, updating, enriching product information.
- Formation of links between goods and categories.
- Marketing tools for analyzing demand and improving customer experience.
- Content segmentation by category. Assigning access to add and edit information to individual users or groups of users.
- Built-in connectors for connecting to different data sources and sales channels.
- Creating integrations in the inriver Integration Framework.
- A fully cloud-based technology that is being deployed on Microsoft Azure.
Additional features
A “clean” PIM system. Additional MDM and DAM features are not available.
Flexibility and scalability
It is positioned as “the only product in the industry with an elastic scalable model”.
- It quickly adapts to changes in business and consumer behavior due to a flexible entity structure.
- Scales attributes, making it easier to enter new markets and sales channels.
- It increases the volume of upsales through a model that takes into account the hierarchy of goods and the relationship between individual products.
Who is inriver suitable for
Inriver is designed for companies operating in the B2B and B2C segments, primarily those that focus on online channels.
License cost
SaaS product. The cost depends on the amount of data storage for your products and the estimated load on the servers. The starting price is 55,000€ per year, the inriver Evaluate system for working with the “digital shelf” is paid separately.
Pimcore
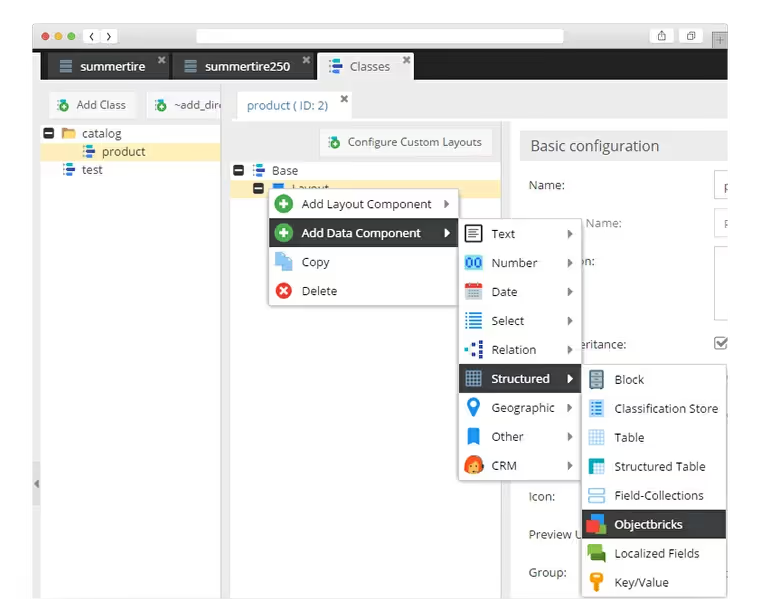
Pimcore — PIM/DAM/MDM system and E-commerce platform that is suitable for managing complex catalogs with a multi-level hierarchy and multiple relationships between products.
Pimcore functionality
- Data modeling.
- Data management.
- Data quality control.
- Integration with external systems for fast data exchange.
- Managing the flow of information, enrichment, and unloading through standardized processes.
- DAM functionality.
- Multichannel publications.
- Creating entities.
- Complex attribute inheritance.
Enterprise Subscription features
- Content management taking into account the specifics of channels and audiences.
- An internal portal for tracking product marketing information.
- Systematic uploading of product information to more than 2000 channels in suitable formats.
- Automatic translation of product information.
- Integration with marketplaces, a single dashboard for tracking orders from all marketplaces.
- Integration with Microsoft and Adobe products.
- Automated upload of information to printable files (catalogs, advertising and promotional materials).
Additional features
In terms of functionality, Pimcore is a low-code product. This means that individual integrations and business processes for collecting and transmitting product data can be implemented without involving developers — by in-house managers or analysts.
Flexibility and scalability
Pimcore is open source, so it can scale indefinitely.
Who is Pimcore for
The system is suitable for companies of any size and with any number of sales channels. It is considered a good choice for integrators and manufacturing companies. It is especially pleasant that the Community Edition already has sufficient functionality even for very large deployments, can be deployed on enterprise servers and is open source.
License cost
Three rates, the cost depends on the functionality.
1. Free Community Edition does not support PXM/AXM functionality, integration with marketplaces, and additional functions for uploading product information. There is no user support. The number of installations is limited.
2. The monthly cost of the extended version is Enterprise Edition — from 1600€ per month, billed annually. It includes all Pimcore functionality, user support is available, but the number of installations is limited.
3. Unlimited Subscription — the maximum version of Pimcore without restrictions on functionality and the number of installations within one organization. The cost starts from €6,400 per month.
Plytix
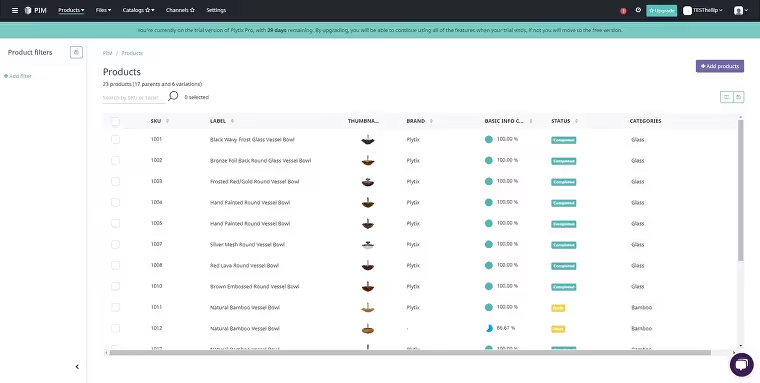
Plytix is a SaaS PIM system with DAM functionality out of the box. Designed for teamwork on product information. The vendor calls the well-thought-out and understandable design of the system one of Plytix's advantages.
Plytix features
- Manage all types of digital data.
- API for custom integrations.
- Unlimited users per company in all plans.
- Differentiation of user roles with the assignment of individual permissions.
- Self-updating smart lists.
- Advanced filtering with built-in AND and OR features.
- Tracking progress in filling out data in product cards.
- 13 types of product information attributes, unlimited custom attributes.
- Set up relationships between items for sale, offers of related items, or sets.
- Managing product variations.
- Mass work with data.
- Fast export to CSV, XLSX, PDF formats.
- Calculated attributes for automatic editing of product information.
Additional features
Plytix offers extensive analytics opportunities: you can receive reports on filters that really matter to you (sales channels, products, categories, dates (Black Fridays), time periods, price ranges). Dashboards are generated directly in the system. Some data is taken directly from Google Analytics.
Flexibility and scalability
In addition to the basic functionality, you can connect:
- Channels module for automatically uploading product information to marketplaces, product comparison services, e-commerce platforms and generating data tables in CSV and XLSX formats;
- Brand Portals module to exchange product information with distributors and retailers with the ability to filter data;
- Product Sheets module to create product tables — a simple interface, ample opportunities to customize the design and structure of tables according to brand requirements, upload to PDF.
Who is Plytix for?
Depending on the chosen tariff, Plytix is suitable for both small businesses and large trade and manufacturing organizations, whose nomenclature includes up to 100,000 SKUs.
License cost
Three pricing plans have been developed for Plytix users.
1. Free. Includes 10GB of cloud storage, up to 1,000 SKUs. There are restrictions on the scope of analytics. There is no limit on the number of users.
2. Standard. €300 per month, €3600 per year, billed annually. Unlimited cloud storage, up to 100,000 SKU. Advanced analytics capabilities. Technical support. Content add-ons.
3. PRO. €1,100 per month, €13,200 per year, billed annually. In addition to the Standard tariff toolkit, support for automatic sales channel feeds, automated generation of tables in CSV and XLSX formats, and updated PDF templates have been added.
All tariff plans include DAM functionality.
Riversand
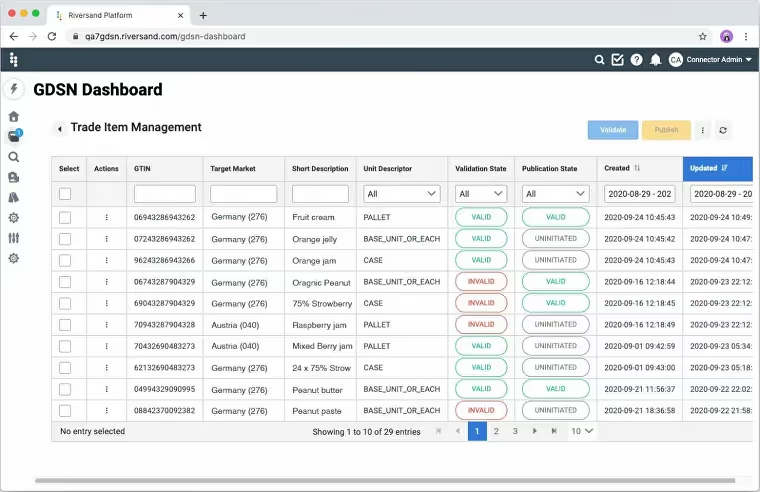
PIM/MDM platform (SaaS), part of the Syndigo ecosystem. It is a leader according to Gartner (Magic Quadrant for Master Data Management Solutions) and Forrester (The Forrester Wave: Product Information Management).
Riversand features
- Automatic download of data from various sources.
- Enriching product data in a single system.
- Data quality management.
- Product data planning, taking into account information about sales drivers in different categories and segments.
- Data management taking into account KPIs and analytical data.
- Media management.
- Automatic generation of recommendations for improving product information.
- Channel analytics, KPIs for promotions, pricing, targeting, segmentation.
Additional features
Separate apps for managing data, tracking, and improving the customer experience. Riversand products have built-in applications for analyzing business information that help identify bottlenecks in processes and data and improve the quality of presence on sales channels.
Flexibility and scalability
The basic functionality of the Riversand platform can be supplemented to meet business needs by downloading connectors, apps for tracking customer experience, and services for improving content from the Riversand App Marketplace. It is also possible to create your own apps for Riversand.
Who is Riversand for?
Riversand is optimal for enterprise-level companies.
License cost
Estimated cost for medium-sized businesses — from €50,000 per year, for big businesses — from 150,000€ per year. The price depends on the number of users who will work with the system and on the required cloud storage capacity for product data.
Sales Layer
Sales Layer is a PIM system with DAM functionality developed in Spain. It is positioned as “the first PIM system developed with a view to marketing departments”. Fully cloud-based.
Sales Layer functionality
- Product information management: loading, enrichment, unloading.
- Direct download of product information from familiar tables.
- Support for multiple language versions of product information (from five in the Premium plan to unlimited in the Enterprise Plus plan).
- Data analysis by language, brand, and product categories.
- Instant creation of individual catalogs for transfer to suppliers, purchasers, etc.
- Assigning roles and distributing access between users.
- Tracking the history of changes in product information: who changed what and when.
- Notifying users about changes.
- Saving product information in backups even in case of technical problems.
- Business processes for working with product information.
- Connectors for integration with marketplaces and IT systems.
Additional features
Automatic translation of product descriptions into 36 of the world's most widely spoken languages: English, French, Chinese, Spanish, etc.
The system automatically retouches downloaded images.
Flexibility and scalability
The basic features of Sales Layer are available to all users. As the catalog expands and the number of sales channels increases (and, accordingly, the need for additional functionality increases: connectors, languages, etc.), the company will have to switch to more expensive plans.
Who is Sales Layer for
A universal PIM system suitable for businesses of all sizes. It is in demand among multinational companies with a catalog size of 100,000 SKUs or more.
License cost
Three rates for companies with different functionality needs.
1. With a tariff Premium Up to 10 users can work in the PIM system. A maximum of 20 connectors can be connected. The maximum catalog size is 150,000 SKU. The limit is five language versions of the information.
2. Tariff Enterprise is designed for companies with a catalog of up to 300,000 SKUs. A maximum of 35 employees can work with information. The system stores a maximum of 10 language versions of product descriptions. Up to 35 connectors are supported.
3. Enterprise Plus — Sales Layer tariff with maximum functionality: the number of users, connectors, SKUs and language versions is unlimited.
Information on the cost of each tariff is available on request.
Salsify
Salsify is not only a PIM system, but also a commerce experience platform, a platform that manages all information about products, prices, customer experience, product promotion experience, digital data, etc.
Cloud-based. Some microservices support multi-tenancy.
Salsify features
1. PIM system functionality: product and product group information management. Editing, tracking, enriching information, uploading to sales channels, complex taxonomy and product relationships. It supports multichannel: information changes in accordance with the requirements of the sales channel.
2. DAM system functionality: centralized loading and orderly storage of digital assets, managing digital assets, synchronizing DAM with existing business processes, checking the relevance of digital assets, etc.
3. PXM functionality: content management in line with consumer interests and expectations.
4. Accumulation and analysis of data to obtain market insights.
5. Integration with marketplaces and sales platforms via social media.
Additional features
A separate product within Salsify is an online chat with a customer who is embedded in a website or online store.
Flexibility and scalability
A microservice architecture was chosen for Salsify; parts of the system support multi-tenancy. This allows companies to optimize the cost of owning the platform. With Salsify, you can use only the services you need and scale the platform itself when your company's growth requires it.
Who is Salsify for
Salsify is suitable for retailers that operate through multiple channels or sell products from several brands. The system is designed for large teams to work and process large amounts of constantly changing data.
License cost
The license costs from $25,000 per year. The price depends on the number of users and their roles, the selected functionality and the capacity of the cloud data storage.
Summary: How to choose a PIM system
At first glance, in terms of PIM functionality, all participants in this review are approximately equal. Yes, each system has certain nuances and additional features that a business may need (although they often coincide). How then can you choose a product that will become part of your business's IT infrastructure if studying the functionality “on paper” does not lead you along this path?
At the stage of choosing a solution, it is important to understand how it will fit into the company's existing IT architecture, how it will change processes, and what problems may arise when integrating or further scaling the system.
IT consulting will help answer these questions. After analyzing your business, existing processes and goals for the coming years, the consultant will reduce the number of possible options to two or three.
The next step is to request a demo from the vendor or its partner. You will be able to see what each system looks like, how it works, how convenient its interface is for you, and which of the declared features you need.
In our experience, these two steps are sufficient to make a decision and start integrating a PIM system, just like other systems in the company's IT infrastructure.